Fuel Dilution
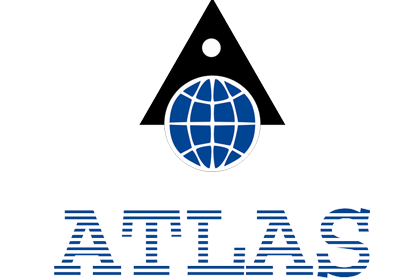
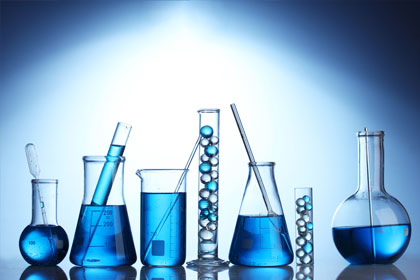
Fuel dilution of the lubricating oil can cause a host of problems to the operating system. As oil is the life blood of a system which maintains it and keeps metal surfaces and their friction separated to prevent and cause wear.
Hence some or all of the following issues can occur if fuel enters the crankcase and contaminates the oil:
- Reduction in viscosity
- Loss of Base number (loss of corrosion protection)
- Accelerated oil oxidation
- Increase in volatility (in extreme cases may lead to crankcase explosion)
- Disruption in oil film strength causing metal friction to contact each other inducing engine wear, especially in the cylinder / ring area
- Varnish formation
- Weakened oil detergency
- Low oil pressure
- Acid formation / corrosion
The causes of fuel dilution can be the result of a large number of reasons:
- Incomplete combustion
- Leaking injectors
- Restricted air filter / bad air to fuel ratio
- Excessive idle time
- Frequent short trip driving
- Cool engine operating conditions
- Incorrect choke setting
- Improper injector timing
- Worn piston rings/excessive blow-by
- Worn seal and gaskets
For practical reasons, depending on the application and operating conditions, a limit of upto 2 % may be considered to be all right provided there is no change in the viscosity. A fuel dilution between 2.5 % to 5.0 % and higher needs caution as it above the limit and is considered to be high and requires immediate attention and action.
Thus excessive idling, frequent start ups of the engine and cold running conditions can lead to minor fuel dilution. But major fuel dilution (excess of 2 %) is due to leakage, leaking fuel injectors and incomplete combustion. In practice about 0.35 % of fuel consumption ends up in the crankcase.
HOW IS FUEL DILUTION DETECTED IN OUR LABORATORY
Fuel dilution is detected in our laboratory by four methods – Viscosity, Flash Point, Gas Chromatography and FTIR.
If the oil is contaminated by Fuel to the extent of over 5 % and above there will be a marked drop in the viscosity.
Flash point of the oil is also a better and simpler way to detect and possibly quantify the percent of fuel dilution. Lubricating oil typically flashes at approximately 215ºC (420ºF) whilst diesel fuel typically flashes at 54ºC (130ºF) so the quantity of fuel can be theoretically estimated by the decrease in flash point when compared to new oil.
The most reliable and accurate method which is used for quantitative measurement and determination of fuel dilution is Gas Chromatography. The testing is based on the boiling point separation of the sample. Its detection limit is as low as 0.1 %. However it should be noted that GC analysis can be time consuming and problematic, especially when used lube oil samples which are mostly dirty are injected in the GC column.
However, GC analysis can be problematic, especially when in-service lubricant samples, which are inherently dirty, are injected onto the column, and this time-consuming technique is far from conducive to real-time monitoring of fuel dilution on an engine test bed.
Method used for Gas Chromatography : ASTM D3524 for fuel contamination & ASTM D3525 for gasoline contamination.
FTIR spectroscopy method is applied in condition monitoring of used or in-service oils for determination of fuel dilution.
Method used for FTIR : ASTM E2412