Glycol / Coolant / Antifreeze
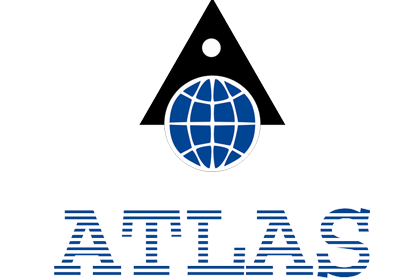
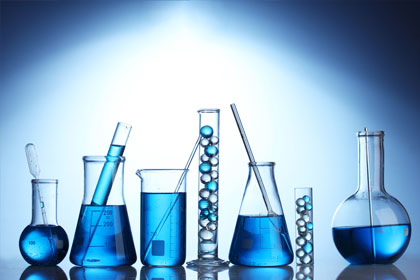
Glycol can leak into motor oils and other lubricating oils in a variety of ways. These include:
- Blown head gaskets
- Cracked block or cylinder head from frozen coolant
- Corrosion damage of cylinder liners
- Cavitations erosion/corrosion of cylinder liners
- Damage or corroded cooler cores
- Defefective or deteriorated seals
- Electrochemical erosion
- Improperly torqued head bolts
- Improperly machined head and block surfaces
- Thermally warped or cracked cylinder heads (from low coolant charge to stuck thermostat)
- Water pump seal failure and weep-hole blockage
Due to so many reasons wherein coolant can leak into the engine, a major deisel engine manufacturer has estimated that about 55 % of all major and catastrophic engine failures are due to coolant leaks. In case of many natural gas engines and diesel engines, the contamination risk is highest during the time the engine is at rest or not operating. At that time, when the engine cools from intermittent use may lead to internal leaks associated with thermal creep, like at the cylinder head where there is a risk of ression or movement from gasket seals. Also when the engine is at rest high hydrostatic pressure of the coolant in relation to the engine system compounds the risk which can lead to slug feeding of the coolant into the lubricant.
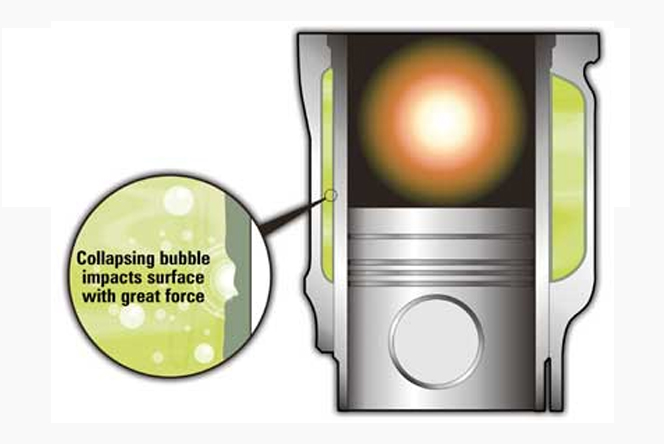
Schematic of Cylinder Liner Cavitation Corrosion
Also another common source of leakage of coolant in the engine with wet cylinder liners occurs due to vaporous cavitation which is associated with a chmical / mechenical perforation of the liners. This happens when the liners on the load side vibrate violently and vigorously to the rhythm of piston movement, compression and combustion. This violent an vigrous movement creates a pressure in the system. As the combustion chamber fires, the vapour bubbles implode at the speed of sound causing fluid jets and surface pressure as high as 50,000 psi. Such focused and localized energy can literally blast small holes in the protective oxide film on the liner wall which is similar to vaporous cavitation in hydraulic pumps.
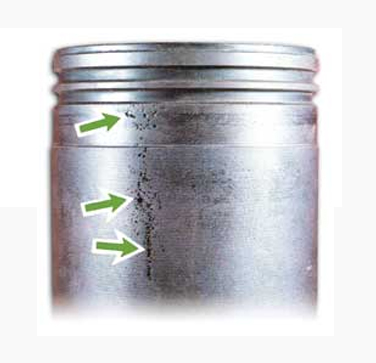
Cylinder Wall Cavitation Erosion
Harm Caused by Glycol-Contaminated Lubricating Oil
When Glycol / Coolant / Anti-Freeze mixies with lube oil it means bad news. Also along with glycol, coolant water also enters the lube system which means that we have a double intensity of the problem. And ofcourse it creates problems and damages, for example, the main and connecting rod bearings may become darkened, almost blackish charcoal in apperance when glycol has invaded and contaminated the engine.
Hydraulic Lock
As mentioned above coolant contamination could erode and corrode the walls of cylinder liners with resultant pinhole perforations. When an engine is not operating, the combustion chamber within the cylinder can be flooded with coolant as it leaks through these pin holes. Later, at the time of starting / cranking of the engine, the lack of compressibility of the coolant can cause hydraulic lock. As the coolant has no exit point and has nowhere to go, rod, rings and bearings faillure is possible.
Acid Formation and Bearing Damage
When an engine operates under normal conditions, coolant – ethylene glycol oxidizes to form organic acids such as:
- Glycolic acid
- Oxalic acid
- Formic acid
- Carbonic acid
These acids contribute to other effects which are described later. The very fact that these acids are present in the oil can damage bearings and other surfaces where friction takes place. Their presence can:
- Tarnish cupric metals of bronze and brass
- Create pit marks on surfaces of tin/lead overlay of journal bearings
- Generate rust on iron and steel surfaces
- Corrode engine steel and copper surfaces
Loss of Dispersancy and Filter Plugging
As a result of coolant contamination, the resultant acids and associated water that which mix into the oil will effect soot dispersancy even if there is initial low soot in the oil. The filters start getting plugged due to deposits due to coolant or water in the crankcase. Due to this there is an accelation of soot and a chain reaction of linked failures can occour like :
- Sticky sludge deposits on valve deck surfaces
- Carbonaceous deposits on ring grooves, bearings, pistons, valve train, etc.
- Loss of antiwear protection
It is even possible that if new oil is added without a system flush, the chain reaction of soot associated with glycol and water will generate a new beginning and again cause sludge and deposits resulting in plugging of the new filter again.
Following is the summary of this chain reaction:
1. Glycol / Anti-Freeze / Coolant leaks into the crankcase lube oil.
2. Acids, deposits and precipitants form as glycol, coolant additives and oil additives react.
3. These insolubles start plugging the oil filter.
4. Concurrently and simultaneously, the acids and water associated in the coolant disrupt soot dispersancy causing a dumping condition causing more sludge and insolubles to form.
5. This results in the filter getting plugged with the glycol transformation by-products and coagulated soot formation.
6. Now the oil and filter are changed (typically around 10 percent of the old oil remains, either in the oil pan or oil stuck to engine surfaces). The new / fresh oil (with detergents and dispersants) mobilizes the soot and sludge, carrying it once again to the filter.
7. And once again, the filter becomes plugged even though the coolant leak is fixed.
Oxidation and Viscosity Change
Glycol contamination causes a reaction with the oil due to ingress of water and air / oxygen in the oil and agressively promotes the formation of oxidation of the lubricating oil. Thus coolant contamination in hydraulic and transmission oils usually shows up as an increase in oxidation.
Glycol contamination along with water contamination causes the viscosity of the oil to substantially increase as it is compounded with the oil forming deposits, higher soot, coagulation of oil which tends to thicken the oil.
How Glycol is Detected in our Lab
Commercial oil analysis labs deploy a number of different test methods and instruments to detect and measure glycol concentrations in used lubricants. The effectiveness of these techniques varies considerably, and for this reason, a discussion that compares and contrasts them is warranted. To this end, the three most common methods used by oil analysis labs are discussed below:
Testing of Glycol
The testing of oxidation is done in our laboratory by using (FTIR) Fourier transform infrared spectrometer, which can be coupled with Water / Moisture Content Test, Soot and Viscosity to determine the extent of glycol contamination and degradation of the oil.
Method of Testing
As per ASTM E2412 : Standard Practice for Condition Monitoring of Used Lubricants by Trend Analysis Using Fourier Transform Infrared (FT-IR) Spectrometry.
Testing Equipment used by us in our laboratory: PerkinElmer make FT-IR Spectrometer model Spectrum 65.
A typical FTIR graph in which glycol contamination is shown and determined.
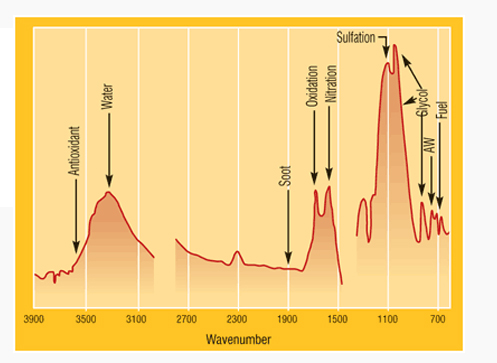