Soot
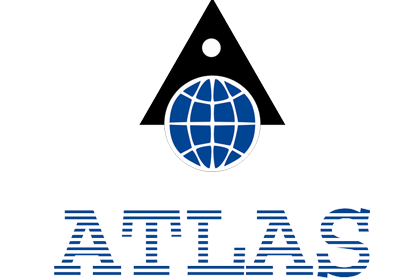
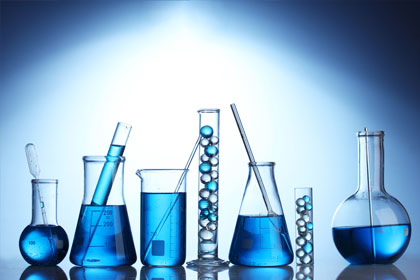
During the diesel engine combustion process, soot particles are produced and are either exhausted into the atmosphere or absorbed by the engine's lubricant. Soot-contaminated lubricant has been shown to produce significant amounts of engine wear. The main mechanism of soot-related wear is through abrasion, but, at increased levels of soot content in the lubricant, starvation of the contact can occur, which can increase wear further. High concentrations of soot can increase the local acidic level and, around the piston where high temperatures and volatile gases coexist, corrosion may also occur.
Excessive soot formulation in oil can be caused by a number of factors. Worn out rings or injectors, excessive idling, poor fuel spray patterns and incorrect air-fuel ratios are major causes of soot formulation. A faulty fuel nozzle may spray more fuel than desired, increasing the fuel-to-air ratio and causing incomplete combustion and soot accumulation, or the air filter may become clogged, decreasing air supply and increasing the fuel-air ratio.
Soot particles are spherical in shape and 98 percent carbon by weight. They are a very small size of around 0.03 microns, but they often agglomerate to form larger particles. Although the majority of soot produced during combustion exits through the exhaust, some passes through the rings of the combustion chamber and enters the engine oil. As long as these soot particles remain suspended in the oil and are not allowed to agglomerate, they pose little risk to engine parts. It is up to the motor oil's dispersants to keep soot particles dispersed. However, in high soot conditions, dispersants can become quickly depleted.
High soot load conditions lead to a loss of oil dispersancy as an oil's dispersant additives are consumed. As dispersancy is lost, soot particles agglomerate and form larger particles that build up on engine surfaces. This soot and sludge eventually impedes oil flow, and can also form on oil filters, blocking oil flow and allowing dirty oil into the engine. In addition, high soot levels within a motor oil increases viscosity, further impeding oil flow and increasing engine wear. Anti-wear additive performance is also affected in high soot conditions as additives are gradually removed from the oil by absorption to soot particles, leading to increased wear and premature engine failure.
Another negative effect of high soot conditions is the formation of carbon particles on the piston ring grooves, causing degradation of the oil seal between the ring and the cylinder line and abrading the ring and liner. As the gap between the ring and liner increases, combustion byproducts such as gases and unburned fuels blow into the crankcase, a problem known as blowby, eventually causing expanding gases to lose ability to push the piston down and generate the power necessary to propel the vehicle. Horsepower is lost and fuel efficiency decreases. Ring sticking and poor heat transfer from the piston to the cylinder wall can also result.
The effects of soot are also know to cause:
- Combustion efficiency is directly related to the soot generation rate. Poor ignition timing, restricted air filter and excessive ring clearance cause high soot load. Combustion problems are not solved by an oil change.
- New diesel engines designed for lower emissions have higher injection pressures. This corresponds to increased sensitivity to abrasive wear (for example, from soot) between rocker, shaft and rocker bearing and can lead to rocker arm seizure. New exhaust gas recirculation (EGR) units on diesel engines amplify the amount and abrasivity of soot production.
- Viscosity increases with soot load. However, high dispersancy associated with some modern engine oils may increase viscosity with soot even more. High viscosity corresponds to cold-start problems and risk of oil starvation.
- Soot and sludge in engines deposit or separate from the oil in the following areas, all presenting risks to engine reliability including rocker boxes, valve covers, oil pans and head deck.
- Deposits on engine surfaces interfere with combustion efficiency and fuel/oil economy.
- Soot polishes off protective antiwear soap films in boundary zones such as cam and cam-follower zones.
- Carbon jacking from the buildup of soot and sludge behind piston rings in grooves can cause rapid wear of rings and cylinder walls. This can cause broken or severely damaged rings during cold-start conditions.
Soot Load Measurement
Measurement of soot can be accomplished using a number of different methods. Below is a general review of each:
- Thermogravimetric Analysis (TGA) - This widely accepted technique provides the most accurate estimate of the concentration of soot as a percent by weight. The test involves progressively heating the sample in a nitrogen-rich atmosphere over time to vaporize volatile fractions until the weight of the sample levels off, typically occurring at around 600º C. Then, the nitrogen environment is replaced by air and the temperature is further raised allowing the oil to oxidize until the weight again stabilizes. Soot concentration is then calculated by subtracting the weight of the volatile ash components from the weight of the original sample. While this technique is accurate, it is strictly a research level laboratory method and is very expensive, usually costing around $200 per test.
- Infrared Analysis - Infrared Analysis has become very popular for measuring soot concentration. Results seem to correlate very well with TGA and the technique is relatively low cost, especially with the proliferation of labs now offering Fourier Transform Infrared (FTIR) analysis. There are also several reasonably priced on-site instruments available for soot measurement (see the Wilks Infracal Soot Meter reviewed in the September/October 1998 issue of POA). Essentially, soot absorbs infrared energy. Unlike many parameters measured with FTIR, soot creates a broadband change in absorption (baseline shift). So, FTIR instruments generally search for soot in 2000 wavenumber region. That region is relatively clear of interference from other oil constituents or contaminants making soot measurement relatively easy. The primary interferences related to this method include the disproportionately increasing absorption of infrared energy as soot particles increase in size, and other particles, like dirt, also absorb broad-band infrared energy and are indistinguishable in measurement from soot.
- Insolubles Test - This test involves the separation of insolubles from the oil after it has been mixed with various solvents like pentane and toluene. The pentane or toluene insolubles are removed by high-speed centrifugation or by filtration onto a membrane disc. When centrifuged, the insolubles are measured as either mass or volume. When filtered, the weight of the new filter is subtracted from that of the prepared filter to determine weight. The technique is relatively inexpensive and very well established. The main drawback is that all insolubles are measured together, not just the soot. Also, the solvent selected affects the outcome. If pentane is used, organic oxides are included in the measurement of total insolubles. Toluene leaves the organic oxides dissolved.
- Light Extinction Measurement (LEM) - The LEM method, researched by Analysts, Inc., method involves casting light at the visible and near infrared frequencies through an object area containing a volume of oil. The light obscured by the oil, as measured by the voltage drop across the object area, is purported to vary with soot concentration. This technique offers simplicity, low cost and a quantitative result. The major drawback lies in the fact that anything that blocks or scatters light is subject to inclusion in the soot estimate (e.g., particles, water, air bubbles, insoluble oxidation by-products, etc.).
- The Blotter Method - This sample method requires only a drop or two of oil on standard chromatography paper. The insolubles separate from the oil and provide a quick visual identification of soot. Further, the paper can be diluted in different solvents to provide an indication of the different insolubles present in the sample. The blotter method offers elegant simplicity, but fails to quantify soot concentration. However, a trained eye can estimate concentration given enough experience; but still, any quantification of soot load must be viewed as suspect.
Dispersancy Measurement
Unlike measuring soot concentration where numerous options exist, measuring dispersancy performance is a real challenge to the analyst. There are two ways to approach the issue: one can attempt to measure the concentration of the dispersant additive itself, or one can measure the dispersancy performance of the oil. For routine used oil analysis, the latter offers a much more promising solution.
While the blotter test offers limited value measuring soot concentration, it provides an excellent assessment of the lubricant's dispersancy performance. An oil that is properly dispersing soot and other insolubles produces an evenly graduated blotter (see Figure 6A). A blotter indicating a high soot load, but even graduation, suggests the oil is still fit for service, but should be watched closely for degradation (see Figure 6B). When dispersancy begins to fail, the insolubles begin to form a dense ring on the exterior of the absorbing oil drop as seen in Figure 6C. Figure 6D indicates the characteristic dense black dot and sharp periphery that forms when the oil completely loses dispersancy performance. From a maintenance perspective, when the ring begins to form around on the exterior of the oil blotter, it is time to look at scheduling a drain. If the black dot is allowed to form, the situation is problematic because the undispersed portion of soot that has deposited upon surfaces will not be removed by the oil change. Often, several changes made at frequent intervals will be required to effectively scour the engine clean. Also, if dispersancy performance degrades at an unusually rapid pace, a more extensive review of combustion and ring performance should be undertaken.
Looking forward, oil analysis programs will have to increasingly combine monitoring of both soot load and dispersancy. Clear limits for soot have not been established. However, according to one industry expert the lubricant manufacturers will need to inform operators of the acceptable condemning limit for soot load. A cautionary limit should also be set at about 50% of the condemnation point. While dispersancy performance will play an increasingly important role in the proactive condition monitoring process to ensure that the lubricant is operating properly, soot load must be carefully trended too. Should dispersancy suddenly fail in a heavily loaded engine, agglomeration occurs rapidly, and it’s too late.
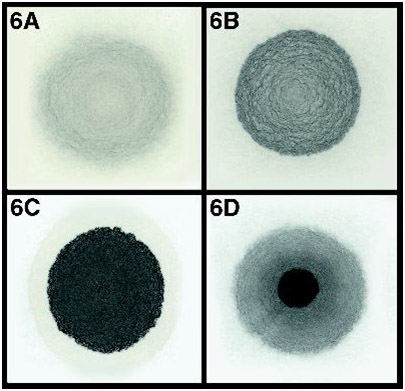
Blotter A shows good dispersancy, blotter B shows high soot load with marginal dispersancy, blotter C shows high soot load and failing dispersancy, blotter D shows failed dispersancy.